So, there’s this material that shows up in all sorts of machines and tools, and most people have no idea what it is. It’s called PTFE, short for polytetrafluoroethylene. Yeah, it’s a mouthful. That’s why people usually call it PTFE—or sometimes by the brand name, Teflon. But here’s the thing: PTFE isn’t just about making frying pans non-stick. It’s kind of a big deal in the industrial world, even if nobody’s really talking about it.
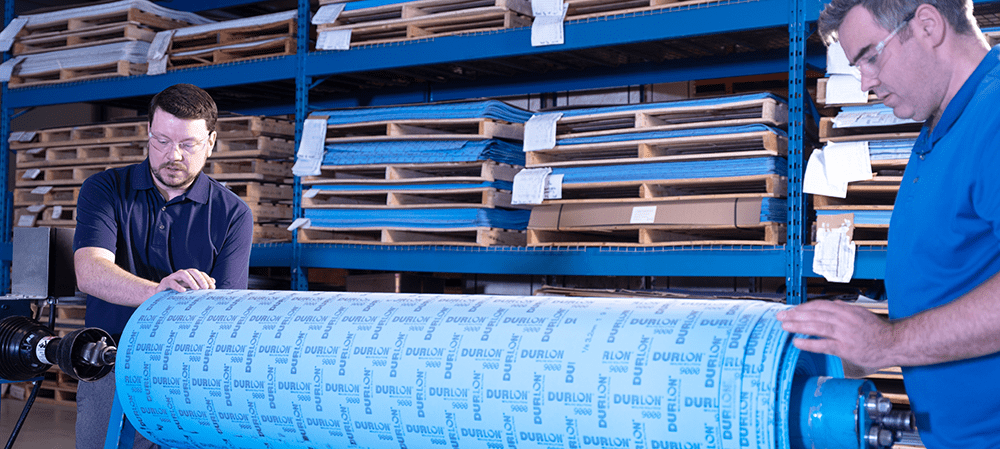
Let’s break it down in a way that actually makes sense.
What Even Is PTFE?
PTFE is a type of plastic, but not the weak kind that cracks or melts in the sun. This stuff can take serious heat, chemicals, friction—you name it. It’s super slippery (nothing really sticks to it), doesn’t rust, and doesn’t fall apart easily. That’s why factories, labs, and engineers all over the world keep using it in places where regular materials would break or wear out fast.
Imagine trying to build a machine that gets super hot or deals with strong chemicals. Most materials would either melt or react. But PTFE? It just keeps doing its thing. That’s one reason so many engineers rely on it.
And for anyone working in manufacturing who needs a solid source, checking with ptfe suppliers can help find high-quality materials that can actually handle the pressure—literally.
Why PTFE Wins in Hard Environments
PTFE works well in places where things get extreme. Not extreme like a movie stunt, but more like super high temperatures, strong acids, or intense pressure.
For example, in a chemical factory, there might be pipes or parts that have to carry harsh chemicals. Metal can corrode. Rubber might wear out. But PTFE? It stays strong, doesn’t break down, and doesn’t absorb anything. That means fewer breakdowns and less downtime for repairs.
In machines that move a lot, parts rub against each other. That rubbing creates friction. Too much friction can mess things up or make machines wear out faster. PTFE’s slippery surface cuts down on all that, helping the parts last longer. That’s one less thing to worry about in a high-pressure setup.
Not Just for Big Factories
While PTFE is definitely a star in industrial places, it’s also used in small devices and gadgets. Think about medical tools, food processing machines, and even parts inside planes. Anywhere there’s a need for something that can stay cool, resist heat, or handle pressure, PTFE can probably do the job.
Even in everyday objects—like cable insulation or water filters—PTFE is hiding in plain sight. It may not be the flashiest material, but it does exactly what it’s supposed to do without causing problems. And that’s kind of the point.
Why Companies Keep Choosing PTFE
One big reason PTFE gets picked over and over again is because it saves money in the long run. It might cost more at first compared to other plastics, but it lasts way longer. That means fewer replacements, less maintenance, and fewer problems later on.
Another reason? It doesn’t react with most chemicals. Some materials can break down or become dangerous when they come in contact with acids or bases. PTFE doesn’t do that. It just stays the same.
It’s also super resistant to water and oils. That’s important in places where machines can’t afford to get clogged or sticky. PTFE keeps surfaces clean, and that helps everything run smoother.
Different Shapes for Different Jobs
PTFE doesn’t come in just one form. There are PTFE sheets, rods, tubes, and even coatings. Each type is used for different things depending on what’s needed.
- PTFE sheets are flat and can be cut to fit into machines as liners or barriers.
- PTFE rods are used to make parts like bearings or seals.
- PTFE tubes can carry liquids without leaking or reacting.
Because PTFE is easy to machine, it can be shaped into all kinds of custom parts. That flexibility is another reason why it shows up in so many industries.
The Science Behind the Slippery
PTFE’s slippery nature comes from its chemical structure. Without getting too deep into science class, the key is that its atoms are arranged in a way that nothing wants to stick to. That’s why even sticky stuff slides right off.
This “non-stick” ability isn’t just helpful in the kitchen. In factories, it means less material buildup. In machines, it means smoother movement. And in places with tight spaces or spinning parts, it means less wear and tear.
It’s Not Flashy, But It’s Important
PTFE doesn’t get talked about as much as flashy new tech or big machines, but it helps those things actually work. It’s reliable, strong, and kind of low-key. But without it, a lot of the things people depend on every day wouldn’t run nearly as well.
From massive machines in power plants to small valves in medical labs, PTFE does its job quietly and keeps things moving. It’s not there to look cool. It’s there to get the job done—and keep doing it, even when everything around it is hot, rough, or full of chemicals.
Final Thoughts
PTFE might not be a household name, but it’s definitely a behind-the-scenes champion. It handles the jobs that are too tough for most materials, whether that’s in a chemical plant, a high-heat oven, or a high-speed machine. Its ability to resist heat, chemicals, and wear makes it one of the most dependable materials in the industrial world.
So next time someone’s talking about strong materials or smart engineering, remember this slippery little powerhouse. PTFE might just be the MVP nobody’s cheering for—but that doesn’t make it any less important.